Updates on the Weaving Equipments and Process of Carbon Fiber Fabrics
Carbon fiber, known for its high strength, high modulus, high-temperature resistance, corrosion resistance, and excellent fatigue resistance, is widely used in fields such as aviation, transportation, medical, and construction. Particularly in the aviation sector, the lightweight characteristics of carbon fiber composites make them indispensable materials in aircraft manufacturing. With the advancement of technology, Sinotextile continuously adjusts and improves carbon fiber weaving equipment, and the production process of carbon fiber fabrics is also constantly refined to meet the high performance requirements of materials in the aviation field.
1. Carbon Fiber Pretreatment Technology
Before weaving, carbon fiber needs to undergo pretreatment to enhance its weaveability and reduce damage during the weaving process. The pretreatment technology mainly involves impregnating a sizing agent to form a soft and tough sizing film, which enhances the bonding capability of the fibers and improves their physical properties. Sinotextile research shows that using F001# sizing agent as a sizing agent is effective in significantly improving the surface smoothness and softness of carbon fiber, thereby enhancing weaving performance.
2. Integrated Warp-Preparing and Weaving Technology
The types of carbon fiber fabrics mainly include plain weave, twill weave, satin weave, and unidirectional fabric. If traditional processes such as warping, sizing, reed insertion, and weaving are used, carbon fiber is prone to issues like fuzzing, sticking, and breakage, making normal production impossible. Therefore, traditional weaving processes are not suitable for the production of carbon fiber fabrics. The process characteristics of carbon fiber fabrics are that the weaving steps should not be excessive, and the total number of warp ends is relatively small. Sinotextile adopts integrated warp-preparing and weaving technology, modifying the weaving machine based on traditional textile processes. A bobbin rack is set up at the back of the weaving machine, where carbon fiber spools are placed.
Bobbin Rack for Carbon Fiber Spool
The unwinding method of carbon fiber on the bobbin rack uses radial unwinding, with some flexible rotating sleeves installed on the bobbin rack that should have a certain degree of rotational damping. The carbon fiber spools are mounted on the sleeves, relying on the tension of the warp yarn to drive the spool rotation, completing the unwinding of the carbon fiber. The unwound carbon fiber passes through a tension device and is introduced into the weaving machine for weaving. This process helps improve product quality, enhance weaving efficiency, and reduce fiber damage, making it suitable for the weaving of fine, high-density carbon fiber fabrics.
Tension Device
3. Fixed Single Warp Yarn Channel Technology
In carbon fiber weaving, controlling the tension of the warp yarn is crucial. To address issues of uneven tension, overlapping, and tangling, Sinotextile has developed a fixed single warp yarn channel technology. This allows each warp yarn to be fixed in an independent channel, enabling precise control of the yarn state, reducing yarn damage, and improving both the intrinsic and apparent quality of the fabric.
Fixed Single Warp Yarn Channel Technology
4. Weft Yarn Control Technology
The control of the weft yarn also significantly impacts fabric quality. Weft yarn unwinding generally employs axial unwinding, using weft tension to unwind the carbon fiber from the spool along the axis; alternatively, the carbon fiber can be unwound beforehand and placed in a box in a regular, relaxed manner. During production, it is drawn from the box using weft tension for weaving. After the weft yarn is drawn out, it enters a weft storage device or other tension devices. The friction damage to carbon fiber in the weft storage device is considerable, so an elastic clip tension device is generally used to apply a certain tension to the weft yarn. Throughout the weft drawing process, due to the characteristics of the rapier loom, a weft break detection device can be implemented in certain areas to achieve automatic stop in case of a weft break, reducing losses caused by weft yarn issues. The weft drawing process should maintain stable tension and have the capability to compensate for tension in a timely manner to ensure smooth weaving.
5. Other Key Process Points
Warp Yarn Damage Control Technology: During the opening motion, carbon fiber warp yarn is prone to friction damage. Sinotextile selects high-quality steel heddles and employs a smaller heald lifting height to minimize damage.
high-quality steel heddles to minimize carbon fiber damage
Weaving Speed: Excessively high weaving speeds can lead to wear and breakage of carbon fiber, so it is better to be controlled below 180r/min to ensure smooth production.
Moisture Control Technology: Appropriate moisture can enhance the weaveability of carbon fiber and prevent fuzzing and breakage. The relative humidity in the workshop should be maintained between 40%-50%.
Tensile Strength Testing: The tensile strength testing of carbon fiber fabrics should be conducted on a universal testing machine to ensure that the strength in both the warp and weft directions meets standards.
Weft Insertion: Sinotextile uses rigid rapier looms imported from Germany and Switzerland, whose superior weft insertion structure can reduce friction on the warp yarn and improve the quality of carbon fiber fabrics.
Control Panel: with excellent leakproofness to avoid short circuit caused by carbon dust.
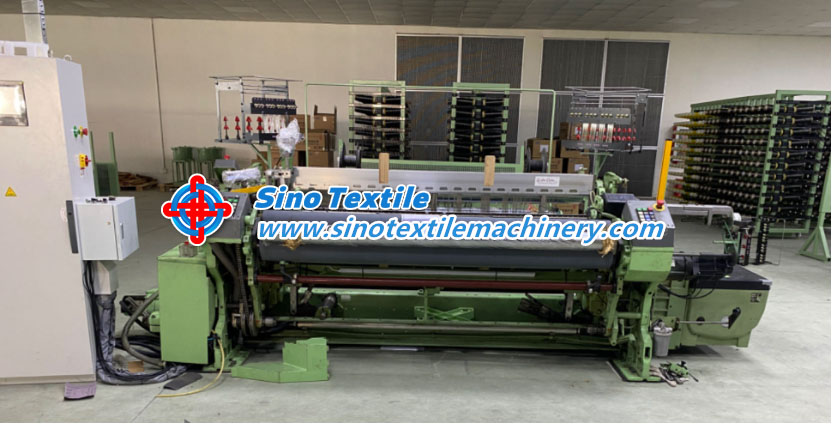